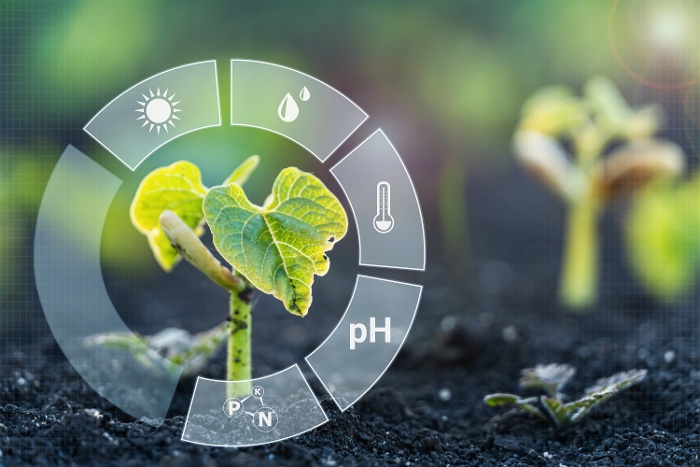
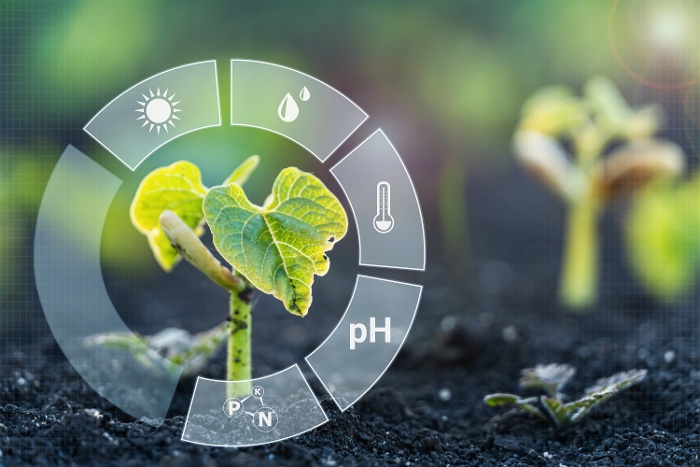
Quick definition: Remote condition monitoring is a process that uses IoT sensors to monitor an asset’s performance in real time. These sensors transmit information like temperature, vibration level, speed, pressure, power, and output to an application, where an operator can analyze it and make decisions. The application can also be configured to send alerts when a piece of equipment’s condition reaches a predefined threshold, allowing operators to prevent breakdowns.
Remote condition monitoring is a staple of industrial manufacturing. Heavy machinery failures are costly, disruptive, and can cause injury or death. Remote condition monitoring has become a go-to solution for reducing these failures and improving safety. The more expensive, mission-critical, or dangerous a piece of equipment is, the more essential remote condition monitoring becomes.
But remote condition monitoring isn’t just for manufacturing. In this article, we’ll look at the benefits and applications of remote condition monitoring—but first, let’s unpack how it works.
How does remote condition monitoring work?
Every piece of equipment will show signs of wear and tear over time. These signs look different depending on the type of equipment, how it’s used, and what components tend to fail first. Additionally, compliance standards, manufacturer warranties, and past experiences with equipment failures may require operators to keep specific conditions below a particular level. All of which determine what kinds of sensors a machine should be equipped with.
An operator won’t always notice changes in conditions or be able to associate them with specific hazards or failures. Remote condition monitoring gives them the visibility they need to see various performance-related measurements are changing over time, and compare them to usual levels or dangerous thresholds.
In its simplest form, here’s how remote condition monitoring works:
- A manufacturer sets thresholds at which specific conditions like temperature are dangerous, indicate that a breakdown is imminent, or indicate that some type of failure has occurred.
- A sensor collects data relating to these specific conditions over time.
- The sensor transmits this information to an application, such as a Supervisory Control and Data Acquisitions or SCADA program in manufacturing.
- When the sensor indicates that a condition has reached a predetermined threshold, it alerts the operator using a notification system.
- The operator decides whether it’s safe to continue using the equipment or if it’s time to have a technician take a closer look. In some cases, they may already know that the equipment needs a specific service.
While the system working behind the scenes can be quite complex, the process is straightforward, making it easy for operators to make more informed maintenance decisions and reduce the likelihood of failures or workplace accidents.
Note: Remote condition monitoring is a stepping stone to predictive maintenance. Check out our article comparing these two approaches to asset management to learn more.
Benefits of remote condition monitoring
While there are a wide range of benefits to remote condition monitoring, it all boils down to three main advantages. Here’s why it’s becoming such an integral part of industries and processes that depend on equipment.
Reduces equipment failures and breakdowns
Breakdowns and equipment failures can disrupt operations for hours or even days depending on the availability of parts and services. In some industries, a single hour of downtime can cost tens of thousands of dollars in lost production. Industrial equipment breakdowns can also be incredibly dangerous to operators, and medical equipment failures can have devastating consequences for the patients who depend on them.
Remote condition monitoring helps reduce these costly and dangerous situations by warning operators when a machine’s condition is abnormal. If the temperature exceeds the normal range and the equipment isn’t safe to run, they can shut it off. If a particular component is vibrating too much, a technician can determine whether something needs to be replaced or simply adjusted.
Keeps machines operating efficiently
While some remote condition monitoring sensors are designed to track conditions like speed and pressure, others monitor performance-related metrics like output. Not only can decreased output be an early warning sign of an equipment failure, but it’s also a clear indicator that the machinery needs some type of service. End users can also define the performance thresholds at which the application should notify them of the decrease. And if other conditions look normal, facility managers can coordinate the maintenance around their operations schedule.
By scheduling repairs and services based on drops in performance, operators and facility managers can keep their equipment running in peak condition for longer.
Lowers maintenance costs
When parts break, it can often damage other components or even cause them to fail. And emergency repairs are always going to be more expensive than scheduled maintenance. Remote condition monitoring reduces your reliance on emergency services and helps you prevent worn-out components from causing further damage (and thus, more expensive repairs).
Improves workplace safety
Some equipment failures aren’t particularly hazardous. But many of them can cause serious harm to the operator, other workers near the machinery, or in the case of medical equipment, the patients that need them.
Remote condition monitoring can also make it easier to comply with safety regulations. Operators often can’t tell if a piece of equipment is under too much pressure, running too fast, or getting too hot to use safely. Your asset management application (such as a SCADA) can alert you when a machine exceeds parameters set by the manufacturer, company guidelines, or government regulations, helping you create a safer work environment.
Note: Predictive maintenance gives you the same benefits as remote condition monitoring, but with the added advantage of machine learning. Using historical performance and maintenance data, predictive maintenance solutions can associate changes in conditions with specific problems, and even automatically schedule services or order parts. Learn more about predictive maintenance here.
Use cases for remote condition monitoring
Remote condition monitoring is already in use in a wide range of applications, and its possible uses are always increasing. Here are some of the main industries that rely on this approach to asset performance management.
Industrial Internet of Things (IIoT)
Most manufacturers report that they’ve experienced unscheduled downtime in the last three years. And collectively, it could cost them as much as $50 billion annually. With how expensive, dangerous, and disruptive manufacturing equipment breakdowns are, it’s no surprise that OEMs are competing to provide better visibility into asset performance.
Manufacturers expect their equipment to come with remote condition monitoring capabilities, and there are solutions for retrofitting older equipment with IoT sensors as well. Whether you’re drilling for oil, running a power plant, building cars, or producing consumer packaged goods, you need to know when your industrial equipment is operating abnormally, so you can minimize the cost to your business, risk to your workers, and disruption to your customers.
Internet of Medical Things (IoMT)
No provider wants to put their patients’ safety (and possibly their own license) at risk by using faulty medical equipment. But sometimes it’s hard to tell when there’s a problem.
A CT scanner constantly moves, so how can you tell when it’s on the verge of moving too much? Medical professionals will eventually hear the loud humming noise that signals when the tube housing is wearing down, and they’ll observe longer tube cooling delays when the scanner is having problems keeping the temperature down—but with remote condition monitoring, they can see these problems sooner, before they start impacting care or causing breakdowns.
Ventilators and other life support equipment have much higher stakes, and they’re sometimes used in a patient’s home rather than a medical facility, making it even more crucial that medical personnel and other caregivers can identify equipment issues early. Remote condition monitoring enables manufacturers to monitor their specialized machines for the first signs of a potential problem.
Smart agriculture
Agricultural operations rely on costly equipment to maintain their razor-thin margins. While some changes in performance can be attributed to the raw materials you’re working with—such as an aging dairy cow that doesn’t produce as much milk as she used to—other anomalies indicate a problem with the equipment. If a component is wearing out in an automatic milking system, that can affect the well-being of your animals, milk yield, or milk quality, all of which would be detrimental to a dairy farm. Tractors are often some of the most critical, expensive equipment on a farm, and remote condition monitoring enables farmers to identify issues before they cause breakdowns.
Farms also use remote condition monitoring to improve crop yield and streamline irrigation. Crop yield monitoring tracks the temperature and moisture level of soil to help maximize crop yield, while smart irrigation uses weather conditions to optimize when watering occurs and avoid wasteful water use.
In any agricultural operation, there are mission-critical assets you can’t afford to be without, and conditions you can monitor to ensure these assets are operating in peak condition.
Improve your remote condition monitoring solution with emnify
emnify is a global IoT connectivity provider. Our specialized SIM cards enable your remote condition monitoring sensors to connect to more than 540 cellular networks in over 195 countries. Wherever you deploy, you and your customers will have the service you need to monitor your assets remotely. And with our network redundancies, we can provide an industry-leading 99.95% guaranteed uptime.
Want to see what emnify can do for your business? Start a free trial or talk to an IoT expert.
Get in touch with our IoT experts
Discover how emnify can help you grow your business and talk to one of our IoT consultants today!
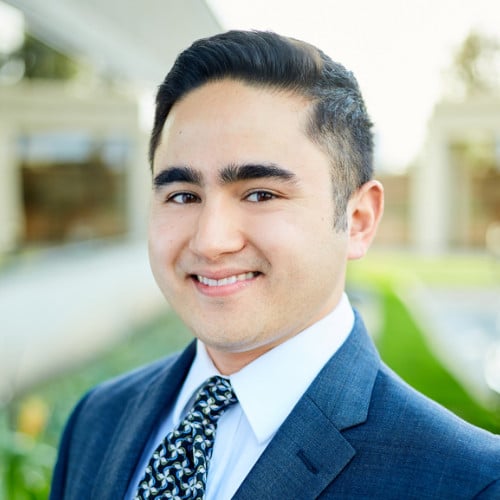
Nathan Schlaffer
More than 7 years of experience translating hi-tech connectivity and SaaS products for Internet of Things into simple and compelling use cases across a broad range of vertical markets from manufacturing to transportation to oil and gas.