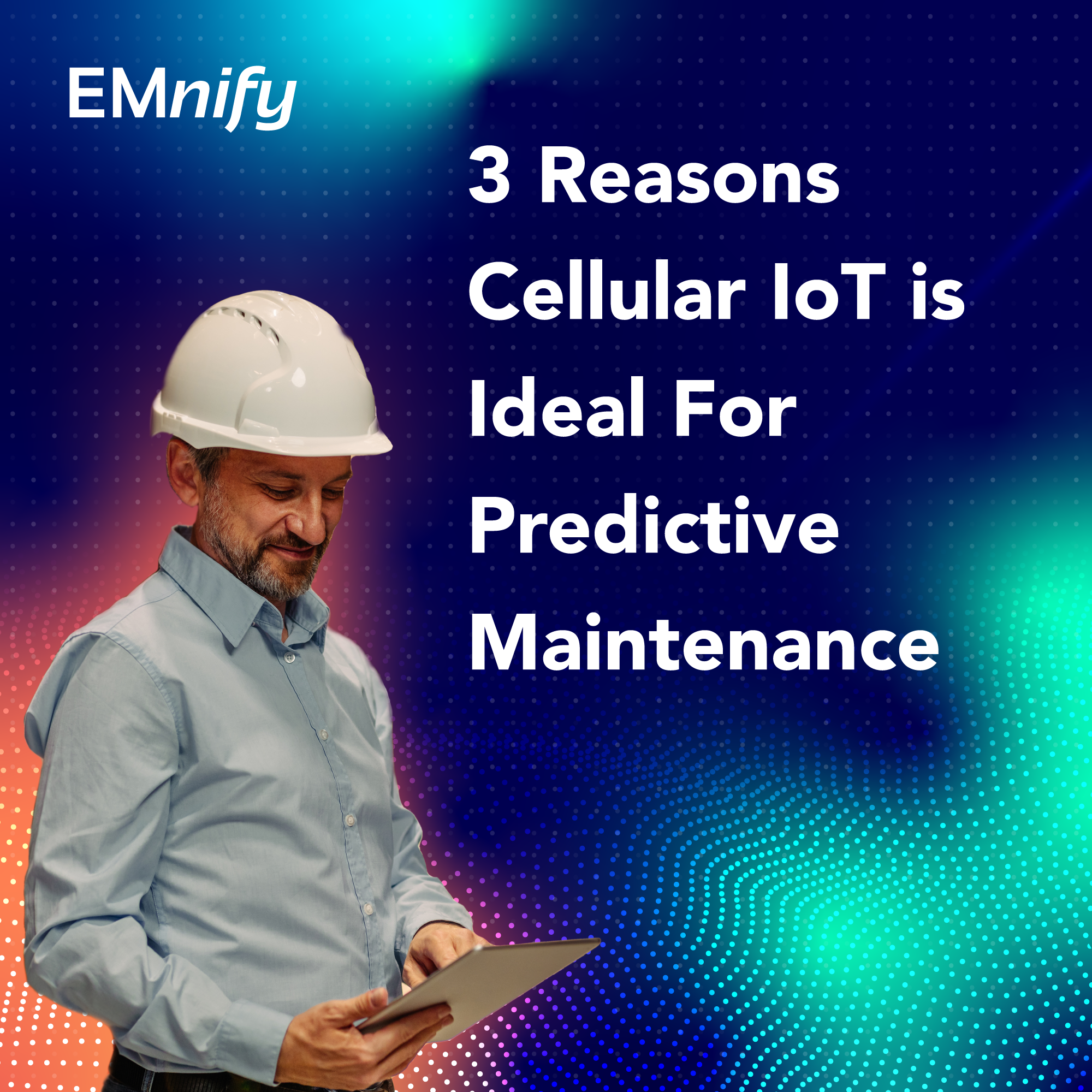
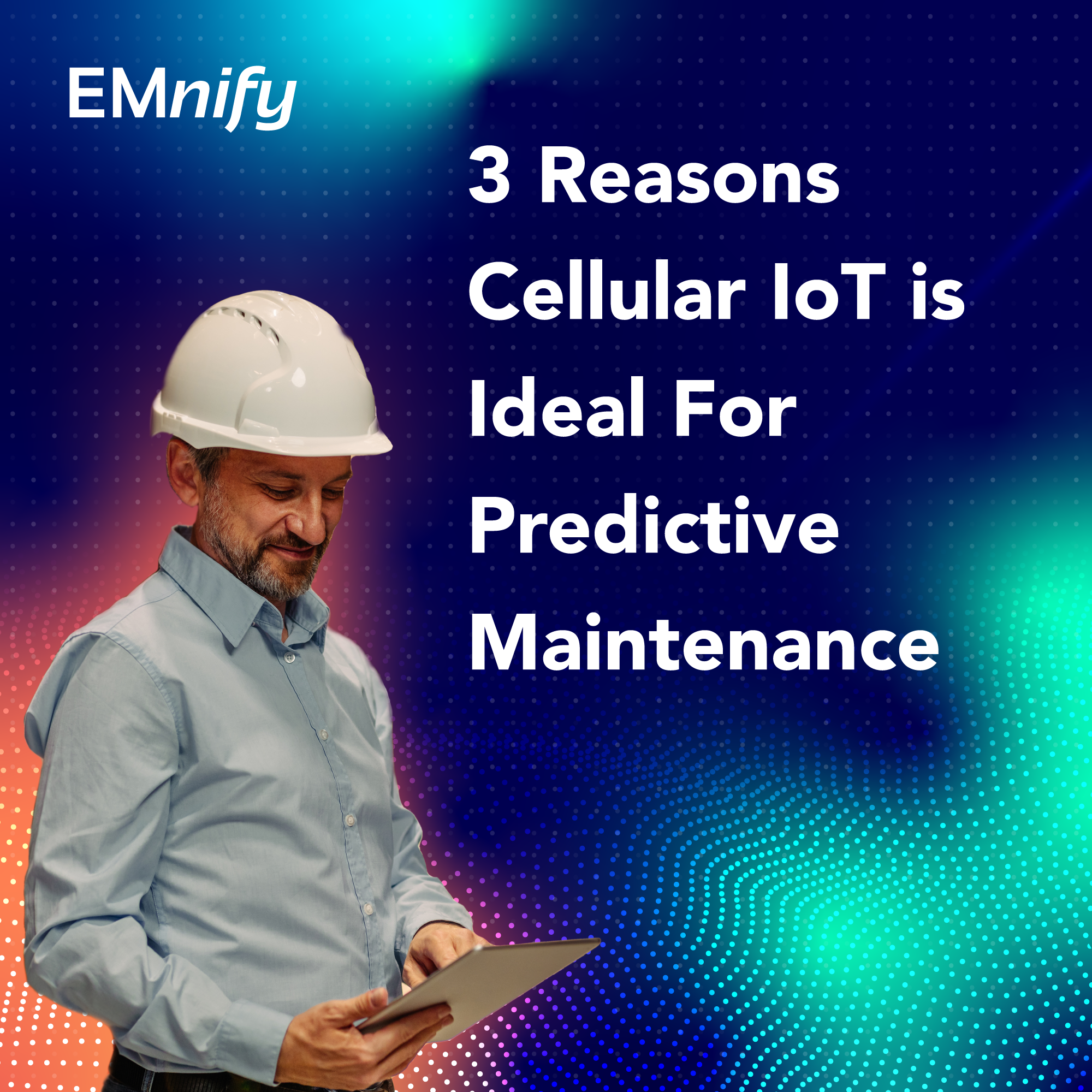
The rise of Industry 4.0 and Internet of Things (IoT) predictive maintenance has led many manufacturers and system integrators to search for more simple, secure, and reliable ways to connect industrial equipment to factory networks. However, deploying effective predictive maintenance applications requires you to overcome significant hurdles – creating reliable machine connections to factory networks, translating between multiple industrial communication protocols, and hardening unsecure factory devices.
The costs of not embedding smart machines with reliable connectivity are great in terms of lost productivity and downtime. Forbes reports the average manufacturer “experiences 800 hours of unplanned downtime annually”and this costs industrial manufacturers approximately "$50 billion annually in lost productivity.” Predictive maintenance can help minimize downtime related costs. According to the U.S. Department of Energy, a robust predictive maintenance program “can yield a 35%-45% reduction in downtime and 25%-30% reduction in maintenance related costs.”
What are the main factors contributing to these challenges and how can you overcome them to build robust smart machines capable of effective predictive maintenance for industrial applications? Read on to learn how cellular connectivity can be the missing ingredient for your successful predictive maintenance deployments.
3 Common IoT Predictive Maintenance Connectivity Challenges
The three main challenges associated with building effective predictive maintenance applications are managing unreliable connectivity, making machines interoperable with industrial networks, and securing factory devices.
1. Managing Unreliable Network Connectivity
The first challenge you face when deploying machines for predictive maintenance is the need for mission critical reliability, and this translates into requiring machines to maintain their connections to factory networks 24/7, 365 days a year. Unplanned network downtime is often caused by unreliable network connectivity due to a lack of network redundancy, poor network connections in remote areas, and consumer-grade networking equipment.
Unreliable connectivity leads to lost productivity and when machines are not producing output, manufacturers have additional costs associated with sending repair technicians on costly trips to troubleshoot machines in person.
2. Managing Network Complexity
In addition to unreliable connectivity, factory networks are becoming more complex with larger numbers of machines, protocols, and security requirements. Compounding the problem is the lack of finding the right personal with the experience to handle this increased complexity.
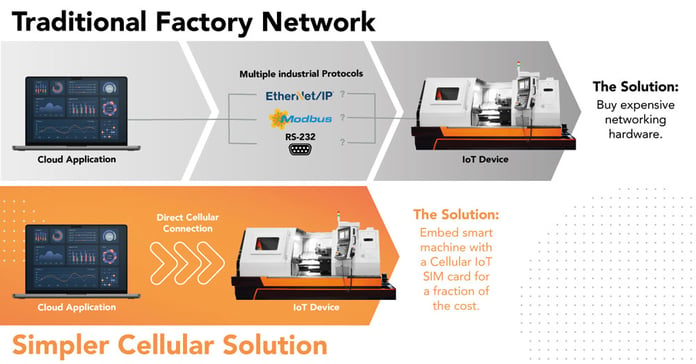
3. Securing Factory Networks
Third, factory networks include assets that were built with operational reliability, but not IT security policies in mind. Many hackers and malicious actors have discovered these security vulnerabilities in IoT and predictive maintenance applications, and purposefully infiltrate them through unprotected machines. Ideally, you can embed IoT devices with IT-level security to fend off cyberattacks, but not interfere with factory production lines or network availability. Besides cyber security, IT managers can also benefit from automated provisioning of SIM cards and a single SIM that supports multiple carriers.
Top 3 Reasons Why Cellular is Ideal for Predictive Maintenance
Reliable, simple, and secure cellular connectivity addresses these challenges facing IoT enabled predictive maintenance deployments. Let’s explore the top three reasons why you should adopt cellular connectivity for predictive maintenance.
1. Maximize Network Reliability with Multi-Carrier Redundancy
You want your machines enabled with predictive maintenance capabilities to operate reliably in a variety of factory settings. To provide robust network reliability, a few mobile virtual network operators have multi-carrier redundancy built into their SIM cards that automatically connect machines to the best available cellular network – serving as a backup network in case one cellular network is down.
Ensure you select SIMs with industrial-grade reliability to survive harsh factory conditions. Network coverage from cellular must also scale to work in multiple countries for machine manufacturers or system integrators who deploy smart machines for predictive maintenance globally. This is one advantage of cellular connectivity versus traditional network deployments – cell tower infrastructure is already in place in most developed countries so you don’t need to invest time or effort into a new network infrastructure to achieve global coverage.
2. Simplify Network Deployments with Cellular
3. Provide End-to-End Secure Communication
IT departments require machine data to be stored and transmitted over encrypted communication channels, especially for IoT and predictive maintenance applications. Consider cellular solutions that have best-in-class security capabilities like OpenVPN, IPSec, IMEI lock, blocklisting, and data threshold limits.
- OpenVPN establishes a virtual private network connection between a machine and a factory network or cloud application – encrypting data and protecting it from cyber criminals.
- IMEI lock and blocklisting prevent unauthorized devices from accessing your customers’ factory networks.
- Data threshold limits limit monthly data usage for devices to a user-set maximum so that people cannot use SIM cards for unintended purposes.
Implementing these security measures satisfy strict IT security policies and provide secure remote access to engineers and technicians troubleshooting machines. A few cellular IoT platforms also offer self-service management of these security measures so you don’t need to pick up the phone and call a mobile network operator.
Adopt Cellular Connectivity for Predictive Maintenance
In summary, IoT predictive maintenance systems require reliable, simple, and secure ways to collect data from smart machines. Cellular connectivity is an essential ingredient that you can utilize for successful predictive maintenance applications because this technology maximizes network reliability, simplifies factory network deployments, and ultimately provides secure end-to-end data communication. Additionally, cloud-based applications, like AWS and Azure, can connect directly with your machines.
About emnify
From reliable connectivity and secure remote access to machines to powerful APIs, automated cloud integration and advanced security features, emnify provides you with all the tools you need to deploy and operate your smart machines for predictive maintenance anywhere and at any scale. Learn more about how we can help your predictive maintenance application here or contact our cellular IoT expert to book a demo and free consultation today.
Get in touch with our IoT experts
Discover how emnify can help you grow your business and talk to one of our IoT consultants today!
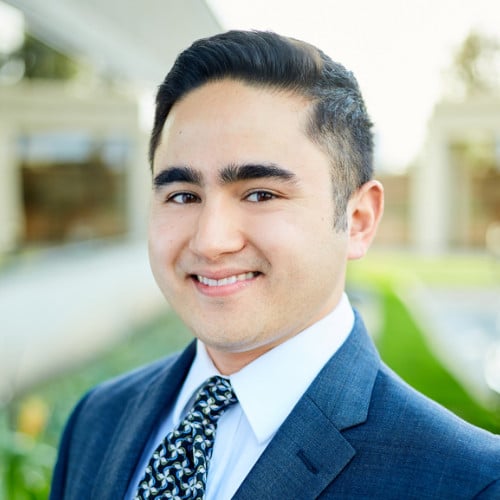
Nathan Schlaffer
More than 7 years of experience translating hi-tech connectivity and SaaS products for Internet of Things into simple and compelling use cases across a broad range of vertical markets from manufacturing to transportation to oil and gas.